A Case Study in Highway Electrical Operations
Creating a robust safety culture is both an art and a science. For organisations in high-risk industries, the challenge lies in translating theoretical safety principles into practical, measurable improvements. This article chronicles our journey in the highway electrical sector from 2020 to 2024, showcasing how we progressed from a compliance-driven approach to embedding safety into every aspect of our operations.
By sharing lessons learned, innovative strategies, and measurable outcomes, we aim to provide actionable insights for other organisations striving to enhance their safety culture. Whether you’re just starting your safety journey or looking to reach new heights, this case study offers a blueprint for sustainable success.
Professor Patrick Hudson’s Safety Culture Ladder provides a framework for understanding organizational safety maturity. Organizations typically progress through five stages: Pathological, Reactive, Calculative, Proactive, and Generative. Each stage represents increasing sophistication in how safety is perceived and managed.
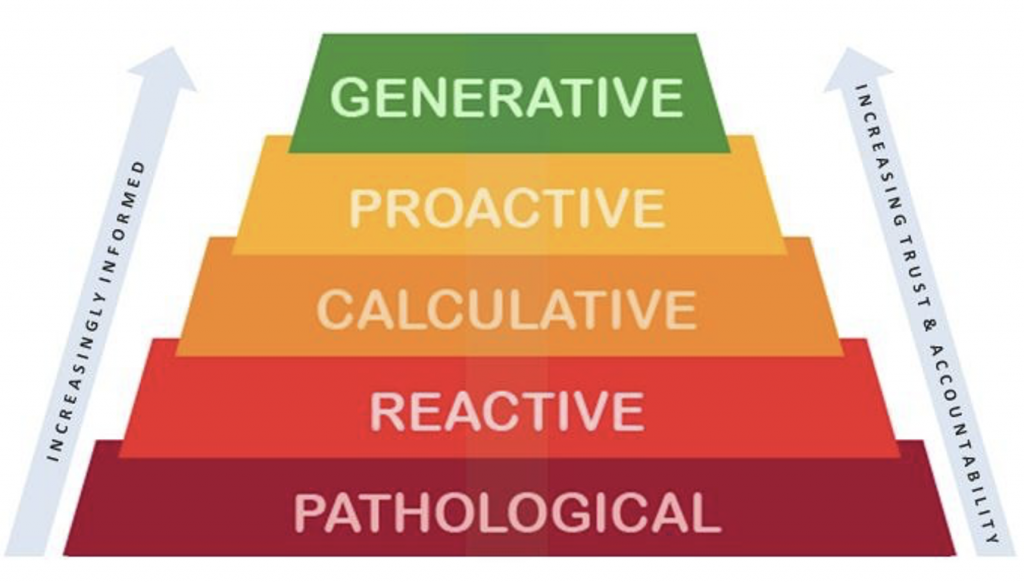
Our journey on the Safety Culture Ladder
In 2020, Electrical Testing exhibited characteristics of a Calculative culture, where safety was managed through systems and metrics. Like many organisations, we had robust processes but needed to move beyond mere compliance. Our journey toward a Generative culture, where safety becomes intrinsic to every operation, revealed several key insights:
Near Miss Reporting Evolution: The traditional interpretation of Heinrich’s Triangle suggests that increasing near-miss reporting automatically reduces serious incidents. However, our experience reveals a more nuanced reality:
2020:
- 36 near-miss reports (0.29 per employee)
- Basic incident descriptions
- Limited root cause analysis (43% completion)
2024:
- 210 near-miss reports (1.68 per employee)
- Detailed narrative reporting
- Comprehensive root cause analysis (89% completion)
This progression demonstrates that quality of reporting matters more than quantity – a key learning for safety practitioners.
Understanding Risk Through the Bowtie Method
To better understand and manage our key risks, we implemented the Bowtie analysis methodology. This approach helps visualise the relationship between:
- Hazards (e.g., underground electrical services)
- Threats (factors that could release the hazard)
- Top Events (the point where control is lost)
- Consequences (potential outcomes)
- Barriers (preventive and mitigative measures)
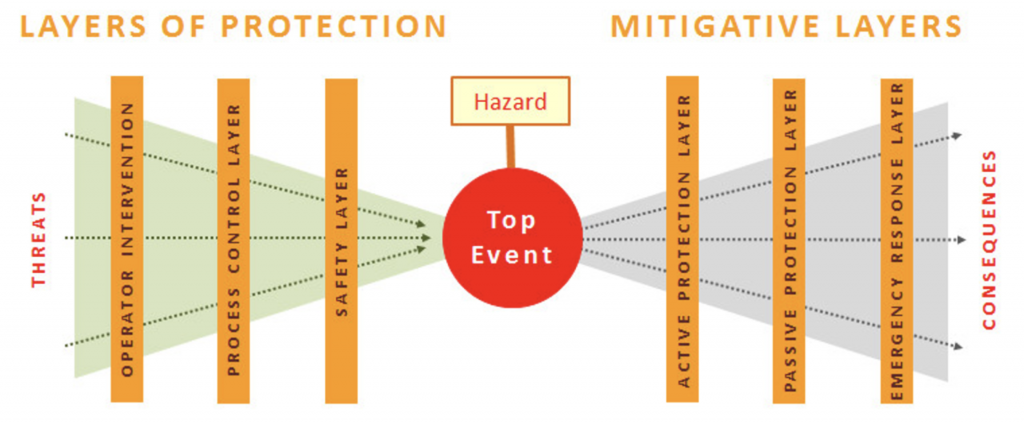
Practical Application of Safety Theory
Understanding Barriers and Controls, The Bowtie methodology helped us identify critical control points in our highest-risk activities. Consider underground service location, one of our primary risk areas:
Preventive Barriers:
- Desktop utility mapping studies
- Site surveys using CAT & Genny technology
- Hand-digging trial holes
- Competency verification system
Each barrier represents a layer of protection, but the key learning was understanding how these barriers interact. For example, while CAT scanning might detect most services, trial holes provide visual confirmation – demonstrating how multiple barriers complement each other.
Stress Management and Human Factors
Safety science teaches us that human performance is significantly influenced by stress levels.
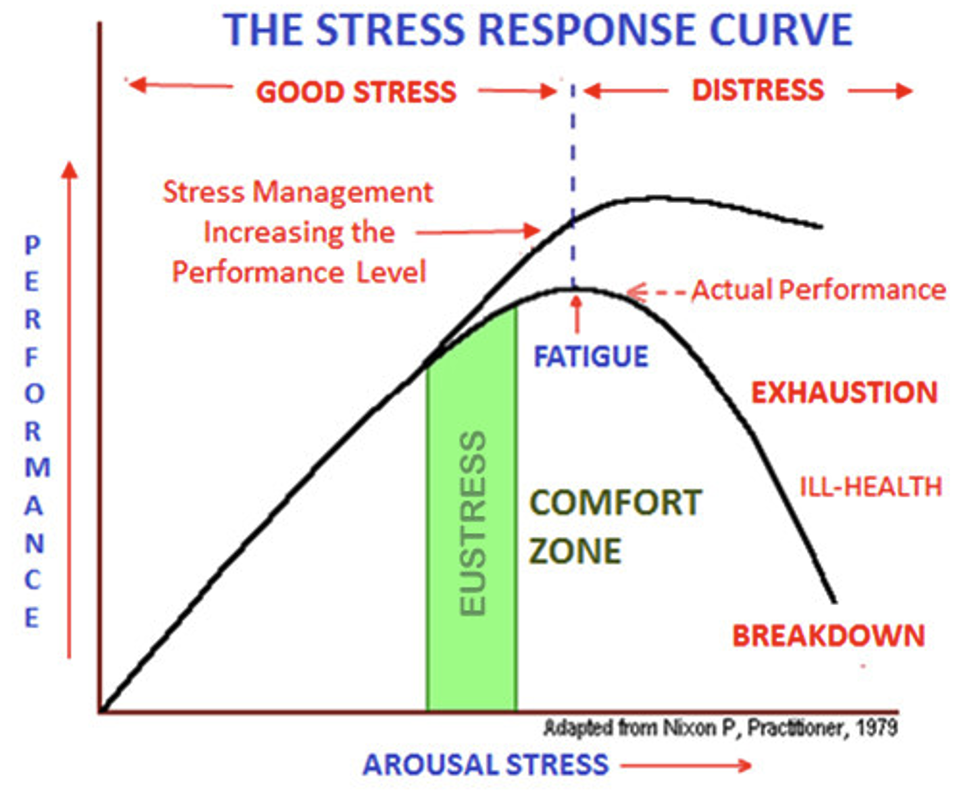
The Stress Response Curve shows that while some stress (eustress) improves performance, excessive stress leads to fatigue and potential errors. In our operation, we observed this through several indicators:
2020:
- Average job completion pressure led to rushed pre-site surveys
- Limited time for detailed risk assessments
- Reactive approach to workload management
2024:
- Implementation of workload planning tools
- Introduction of “Stop Work Authority” without prejudice
- Structured break patterns for high-risk tasks
The Impact of Systems Integration
Example: Underground Service Detection
Moving toward a Generative safety culture required integration of various management systems. This reflects the academic understanding that safety isn’t a standalone function but must be woven into operational processes:
Before: Separate processes for utility mapping, site surveys, and excavation.
After: Integrated system where each stage informs the next:
- GIS mapping data feeds into survey planning
- Survey findings update live risk assessments
- Excavation methods adapt based on cumulative data
This systems thinking approach led to measurable improvements:
- Service strike frequency reduced by 86%
- Near-miss quality reporting improved by 108%
- Preventive barrier effectiveness increased by 92%
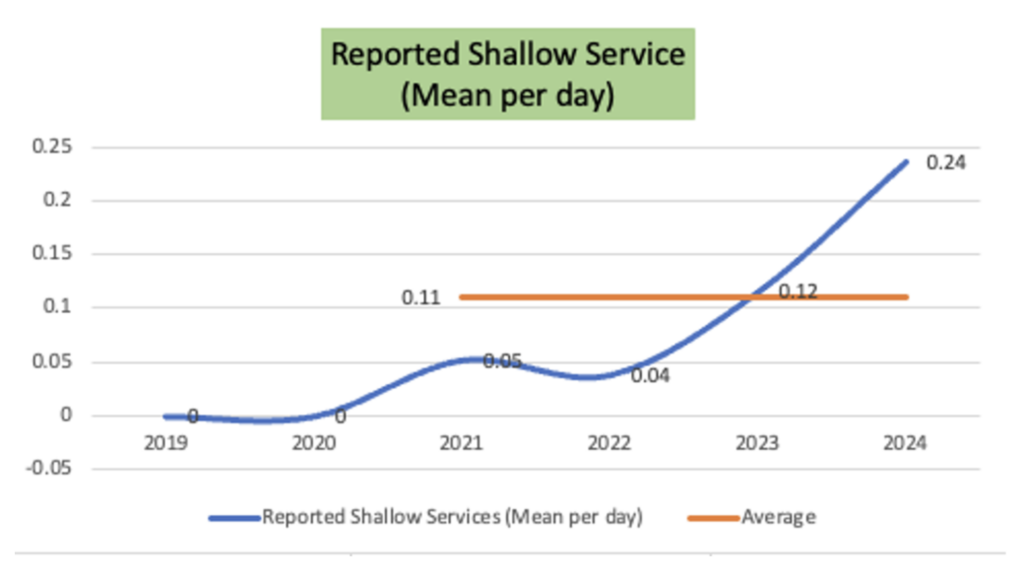
Workforce Engagement and Performance
One of the most important lessons from safety science is that human performance isn’t simply a matter of following rules. Instead, it’s influenced by what safety theorists call ‘Performance Influencing Factors’ (PIFs). At Electrical Testing, we observed how these factors interact in real-world situations.
Consider a typical underground cable location task. In the past, an engineer might face multiple pressures:
- Time constraints from traffic management permits
- Client deadlines
- Weather conditions
- Equipment availability
- Personal fatigue
By understanding how these factors combine, we developed more effective approaches. For example, we introduced a dynamic risk assessment process that specifically considers these human factors. This led to a better understanding of risk management in practice.
Measuring Cultural Change
Traditional safety metrics like Lost Time Injury Frequency Rate (LTIFR) only tell part of the story. Our journey toward a Generative safety culture required new ways of measuring success. We developed what we call “Cultural Indicators”:
- Quality of Safety Conversations: 2020: Primarily focused on rule compliance 2024: Evolved to discuss potential system improvements
- Employee Participation: 2020: 23% of staff actively contributed to safety initiatives 2024: 89% regular participation in safety improvements
- Leadership Engagement: We measured this through what safety theorists call “safety walks” – structured workplace interactions between leaders and frontline staff. The quality of these interactions improved significantly: 2020: Focus on visible compliance 2024: In-depth discussions about risk perception and control effectiveness
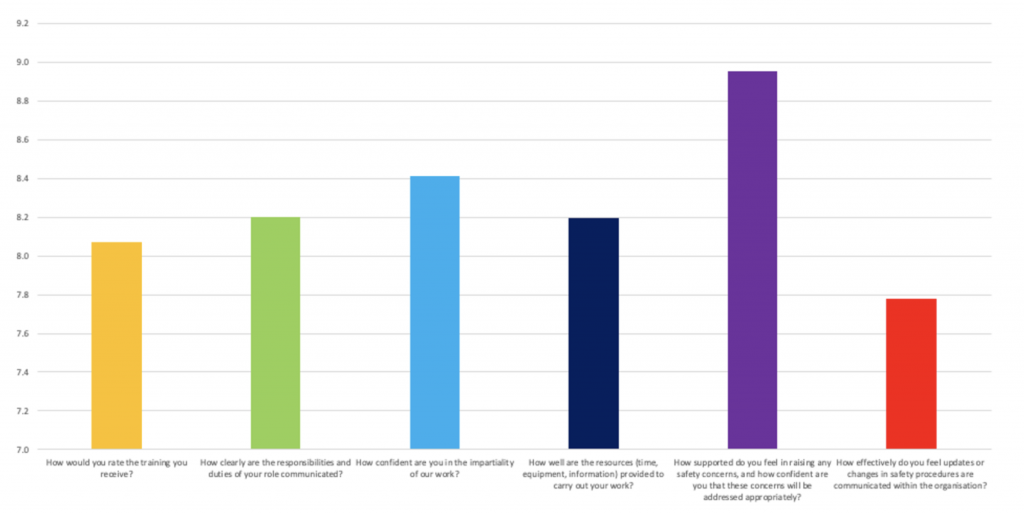
The Business Case for Safety Excellence
Understanding the relationship between safety performance and operational efficiency helps demonstrate why pursuing a Generative safety culture makes good business sense. Safety theorists have long argued that organisations operating at the Generative level of the Safety Culture Ladder typically show excellence across all operational metrics.
Consider how our approach to underground service location evolved. The traditional view might see safety procedures as additional steps that slow down work. However, our data tells a different story:
2020 Process:
- Separate site surveys
- Individual risk assessments
- Standalone safety checks Average job completion time: 4.2 hours
2024 Integrated Process:
- Unified digital platform
- Real-time risk assessment updates
- Collaborative safety-efficiency approach Average job completion time: 3.1 hours
This 26% improvement in efficiency came not despite enhanced safety measures, but because of them. When we better understand and control risks, work flows more smoothly with fewer interruptions.
Understanding Work as Done vs Work as Imagined
Safety science teaches us about the gap between how we think work happens (work as imagined) and how it actually occurs (work as done). By acknowledging this gap, we made several key discoveries:
- Procedural Efficiency: Our engineers found better ways to complete tasks safely when we involved them in procedure development. This engagement led to:
- More practical safety controls
- Improved workflow efficiency
- Higher compliance rates
- Better quality outcomes
- Understanding real-world work patterns helped us improve resource allocation through:
- Better scheduling of equipment based on project needs
- More efficient team deployment
- Improved coordination between teams
Addressing the Diversity of Organisations Within the Supply Chain
One of the challenges in cultivating a generative safety culture lies in collaborating with organisations that are at different stages on the Safety Culture Ladder. Within any supply chain, participants may span the spectrum, from Pathological (where safety is ignored or seen as a hindrance) to Generative (where safety is ingrained into every aspect of operation). This diversity creates both challenges and opportunities that significantly influence the effectiveness of safety initiatives across the supply chain.
Challenges of Cultural Misalignment
- Inconsistent Standards: Organisations in the Reactive or Calculative stages may focus on minimum compliance, leading to gaps in safety standards and practices. For example, a contractor with limited focus on proactive risk management may struggle to meet the requirements set by a client with a Proactive or Generative safety culture. This misalignment can create vulnerabilities in high-risk tasks, such as underground electrical service detection or heavy lifting operations.
- Communication Barriers: When organisations operate at different safety maturity levels, they may lack a shared understanding of safety priorities. For instance, a proactive emphasis on dynamic risk assessments and near-miss reporting may be undervalued by a less mature organisation, leading to resistance or misinterpretation of expectations.
- Resource Inequalities: Smaller organisations or those with limited resources often face difficulty implementing advanced safety systems or training programmes. This disparity can undermine broader safety goals, as even the most advanced systems rely on collaboration across the supply chain.
Opportunities for Safety Leadership
- Cultural Influence: Organisations operating at the Generative stage can act as leaders within the supply chain, demonstrating the tangible benefits of safety excellence. For instance, sharing data on improved efficiency and reduced downtime through integrated safety processes can encourage others to invest in similar approaches.
- Knowledge Sharing: Providing training, mentoring, and resources to less mature organisations can elevate the overall safety performance of the supply chain. For example, we introduced workshops on Bowtie methodology to smaller subcontractors, which helped them identify key barriers in their own operations.
- Collaborative Initiatives: Joint safety programmes, such as shared site inductions or collaborative incident investigations, can bridge cultural gaps. These initiatives not only enhance safety but also foster trust and alignment among supply chain partners.
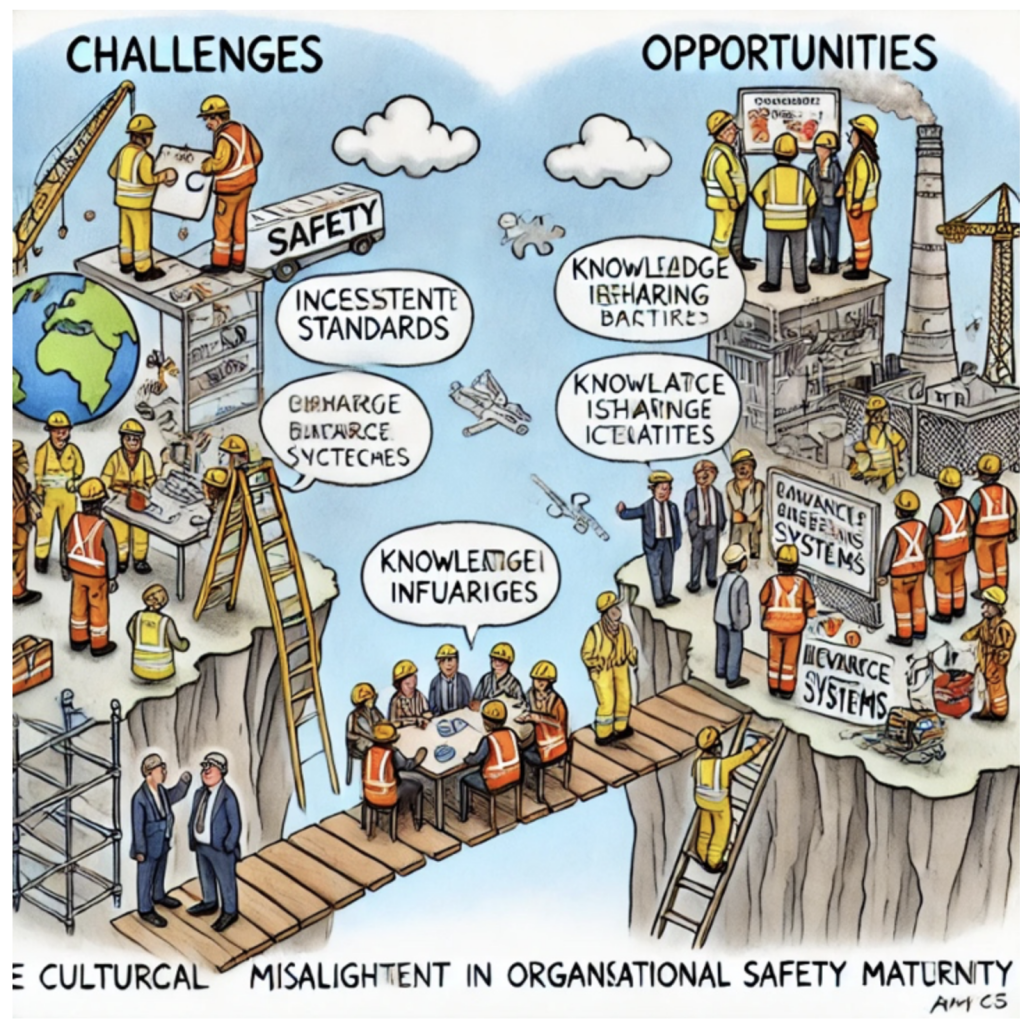
Partnering Across the Ladder
In recent years, Electrical Testing has worked with several partners across the supply chain who operate at various levels on the Safety Culture Ladder. Many of these organisations initially focused on meeting basic compliance requirements, with limited emphasis on broader safety initiatives. Through collaborative efforts, such as joint risk assessment workshops, safety walk discussions, and shared training opportunities, we were able to support their progression toward a more Proactive approach to safety.
A key lesson from these partnerships was the importance of listening and recognising that no single organisation has all the answers. By approaching these collaborations with humility and an openness to learning, we gained valuable insights from our partners’ experiences and perspectives. This was especially evident in industry-specific areas like the Highway Electrical Registration Scheme (HERS), National Electricity Registration Scheme (NERS), and apprenticeship frameworks, where different organisations brought unique challenges and solutions to the table.
At the same time, we were able to share our own knowledge of safety science and practical applications, helping our partners strengthen their preventive measures, improve near-miss reporting practices, and enhance their overall safety culture.
This two-way exchange not only elevated safety standards across the supply chain but also underscored the value of continuous learning and mutual respect. By listening as much as we shared, we fostered a collaborative environment that strengthened both individual organisations and the collective resilience of the supply chain.
Sustainable Safety Excellence and Future Challenges
Safety science teaches us that sustainable safety performance requires more than just good procedures and systems. It demands what Professor James Reason calls “chronic unease” – a constant, healthy awareness that hazards evolve and controls can degrade. At Electrical Testing, this understanding shapes our approach to long-term safety management.
Our journey from 2020 to 2024 demonstrated that becoming what Peter Senge calls a “learning organisation” is crucial for safety excellence. This means:
Understanding Complex Systems: Consider how a seemingly simple task like replacing a street light involves multiple interacting systems:
- Electrical systems
- Traffic management
- Public interface
- Weather conditions
- Equipment reliability
- Human performance factors
Each of these systems contains what safety theorists call “dynamic complexity” – patterns that change over time. Our success comes from understanding these patterns and adapting our controls accordingly.
Future Challenges: As we look beyond 2024, several key challenges emerge:
- Technological Evolution: New technology brings new risks. For example, the increasing adoption of electric vehicles means our engineers now work with charging infrastructure, introducing novel hazards requiring fresh approaches to risk assessment.
- Climate Change Impact: Extreme weather events are becoming more frequent, affecting our ability to work safely. This requires:
- More robust weather monitoring systems
- Flexible work scheduling
- Enhanced equipment specifications
- Adapted safe working practices
- Workforce Demographics: As our industry faces demographic changes, we must:
- Transfer knowledge effectively between generations
- Adapt training methods for different learning styles
- Maintain consistent safety standards across varying experience levels
- Aging Infrastructure: The UK’s street lighting stock presents increasing challenges as it ages beyond its designed lifespan:
- Structural integrity becomes less predictable, requiring enhanced testing regimes
- Electrical systems deteriorate in ways that may not be visible during routine inspection
- Original installation methods may not meet modern standards
- Documentation of historical modifications may be incomplete
- Material fatigue can accelerate unexpectedly
- Multiple modifications over decades create complex fault scenarios
The Path Forward: Safety excellence is not a destination but a journey.
As the challenges of evolving technology, climate change, and infrastructure demands grow, so too must our commitment to continuous improvement. We encourage every organisation to reflect on its own safety culture: Where are you on the Safety Culture Ladder? What steps can you take today to move closer to a Generative culture where safety is instinctive and integrated into every operation?
Begin by engaging your workforce, reviewing your systems, and prioritising human factors. Share your lessons learned and collaborate with industry partners to create a safer, more efficient future. Safety isn’t just a compliance requirement—it’s a driver for operational excellence and a cornerstone of sustainable success.
Take the first step now. Assess your culture, engage your teams, and make safety the foundation of your organisation’s legacy.