The Holistic Approach to Asset Classification: Simon Hobbs, managing director of Electrical Testing goes “Beneath the Surface“.
In the realm of infrastructure management, particularly when dealing with structural assets like lighting columns or utility poles, the term “asset classification” is frequently used. While it may be tempting to focus on a single defect or issue, such as corrosion in the root of a column, this could lead to an incomplete understanding of the risks involved. Let’s explore the complexities of asset classification, and I’ll explain why a holistic approach is essential for accurate and effective risk management.
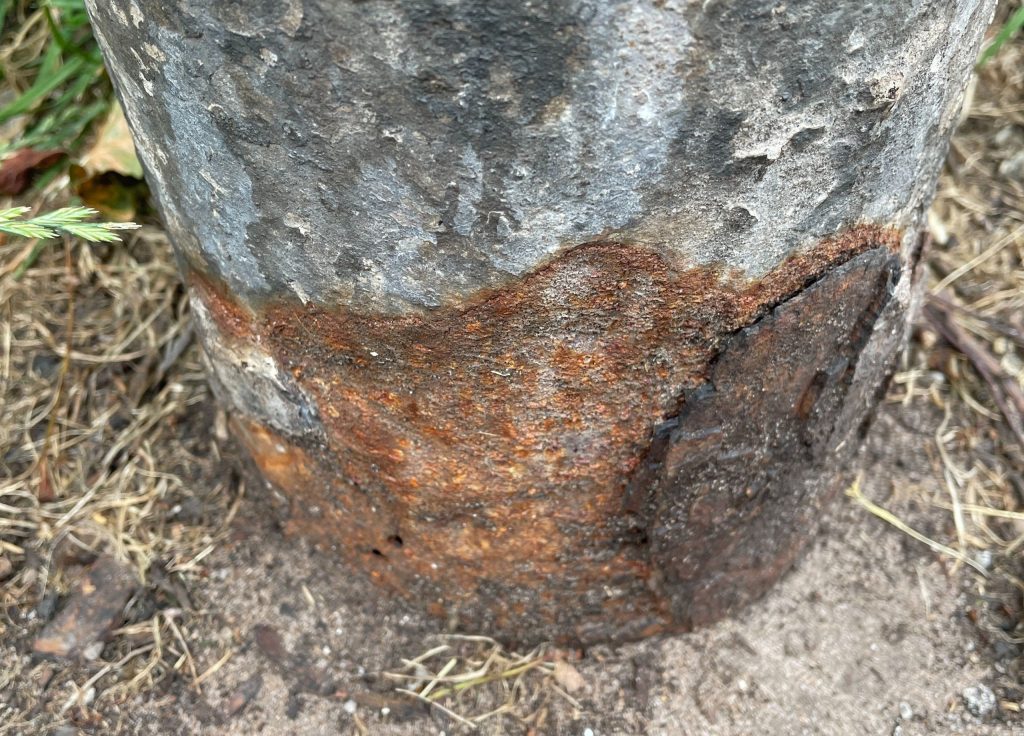
The Importance of a Comprehensive Approach
A single defect or issue, such as corrosion in the root of a column, is undoubtedly important. However, focusing solely on one aspect can lead to an incomplete and potentially misleading understanding of a unit’s overall structural integrity. A comprehensive, holistic approach is essential for accurate and effective risk management. This involves considering a variety of factors, each contributing to the final risk score that dictates the unit’s classification.
The Complexity of Steel Deterioration
Steel, a commonly used material in structural assets, is susceptible to various forms of deterioration, including corrosion and fatigue.
Corrosion is essentially the electrochemical reaction between steel and environmental elements like water and oxygen. This reaction leads to the formation of iron oxides, commonly known as rust, which can weaken the structural integrity of the steel over time. There are different types of corrosion that can affect steel:
- Uniform Corrosion: This is the most common form, where the metal corrodes uniformly all over its surface. It’s relatively easy to detect and manage.
- Galvanic Corrosion: Occurs when two dissimilar metals are in contact, leading to accelerated corrosion of the less noble metal.
- Pitting Corrosion: A localised form of corrosion that leads to the creation of small holes or “pits” in the metal, which can be more dangerous than uniform corrosion due to its localised impact on structural integrity.
- Crevice Corrosion: Occurs in stagnant locations, such as crevices and other areas where debris accumulates.
- Stress Corrosion Cracking: A form of corrosion accelerated by tensile stress, often resulting in sudden failure due to crack propagation.
Corrosion can be managed through various methods like coatings, cathodic protection, and regular maintenance to remove rust and reapply protective layers.
Fatigue in steel occurs due to repeated or fluctuating stresses that are below the material’s ultimate tensile strength. Over time, these stresses can initiate microscopic cracks within the steel, which may eventually propagate and lead to catastrophic failure if not detected and managed. Fatigue is often categorised into three stages:
- Crack Initiation: The repeated stresses cause microscopic imperfections or dislocations within the steel’s crystalline structure, leading to the initiation of a small crack.
- Crack Propagation: Once initiated, the crack begins to grow with each stress cycle. This stage can last for a significant portion of the total fatigue life.
- Sudden Failure: Eventually, the crack reaches a critical size, causing the material to fail suddenly and often catastrophically.
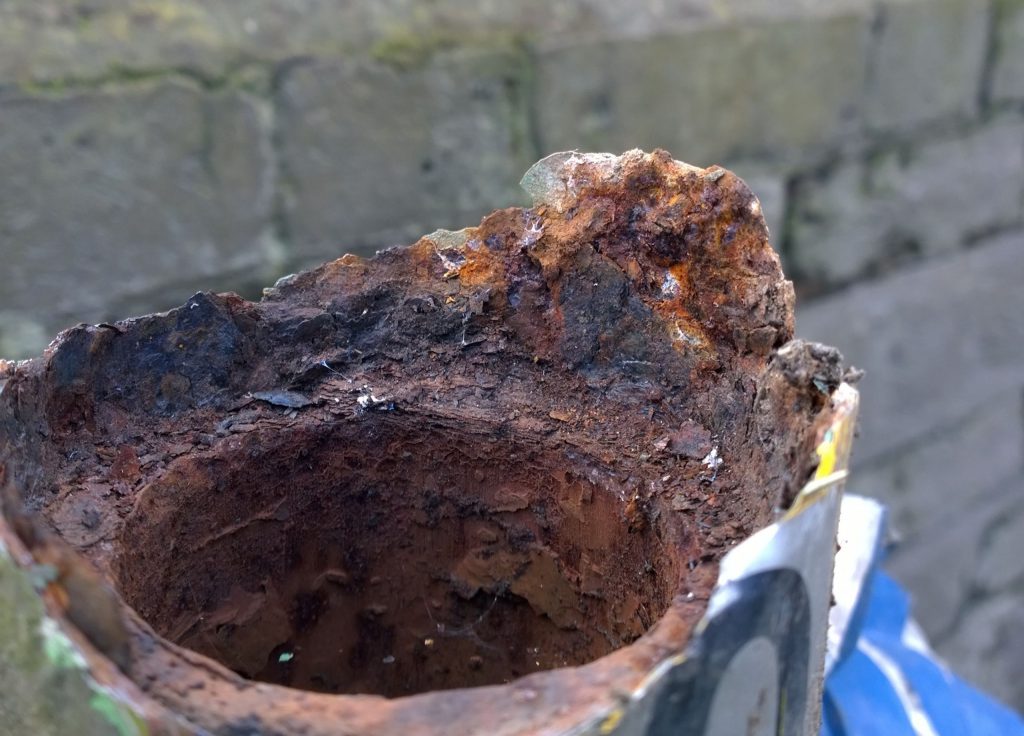
Fatigue can be exacerbated by factors like corrosion (known as corrosion fatigue), poor manufacturing processes, or the presence of notches and other stress concentrators.
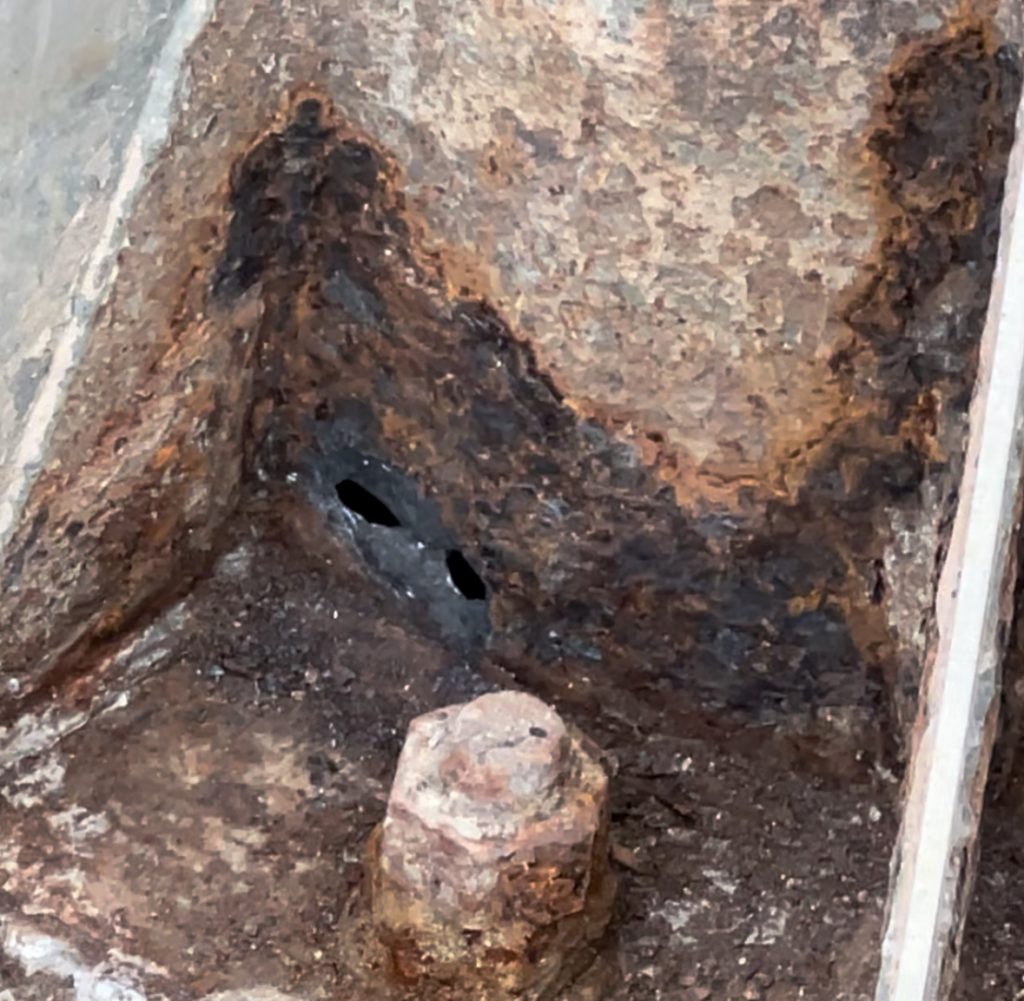
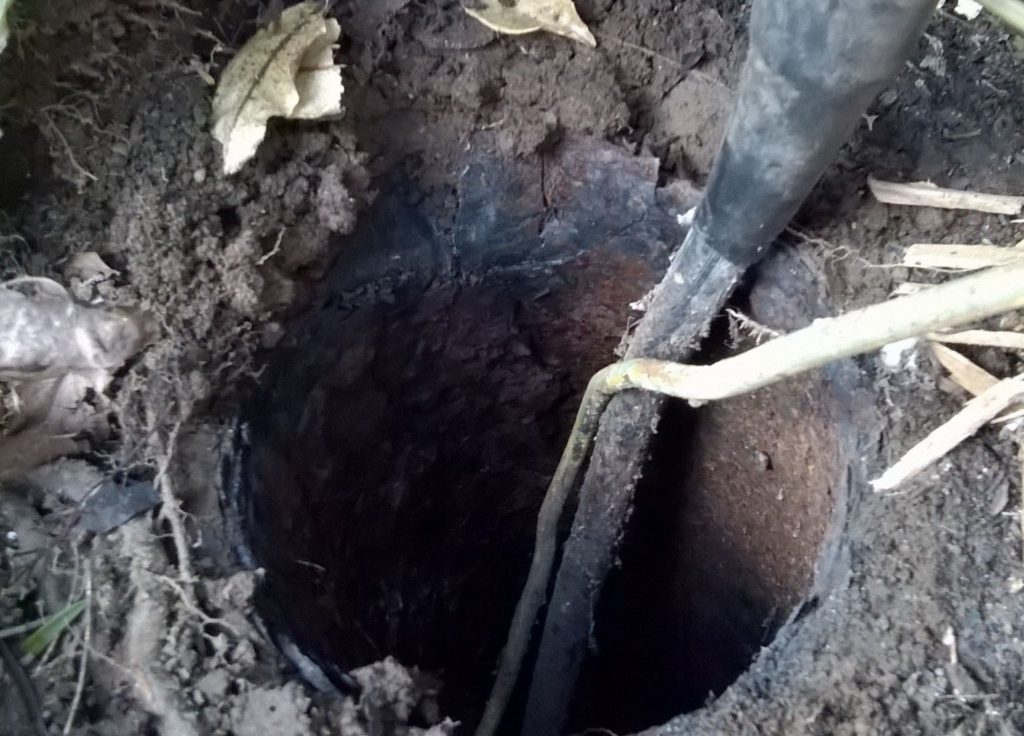
A Testing Time
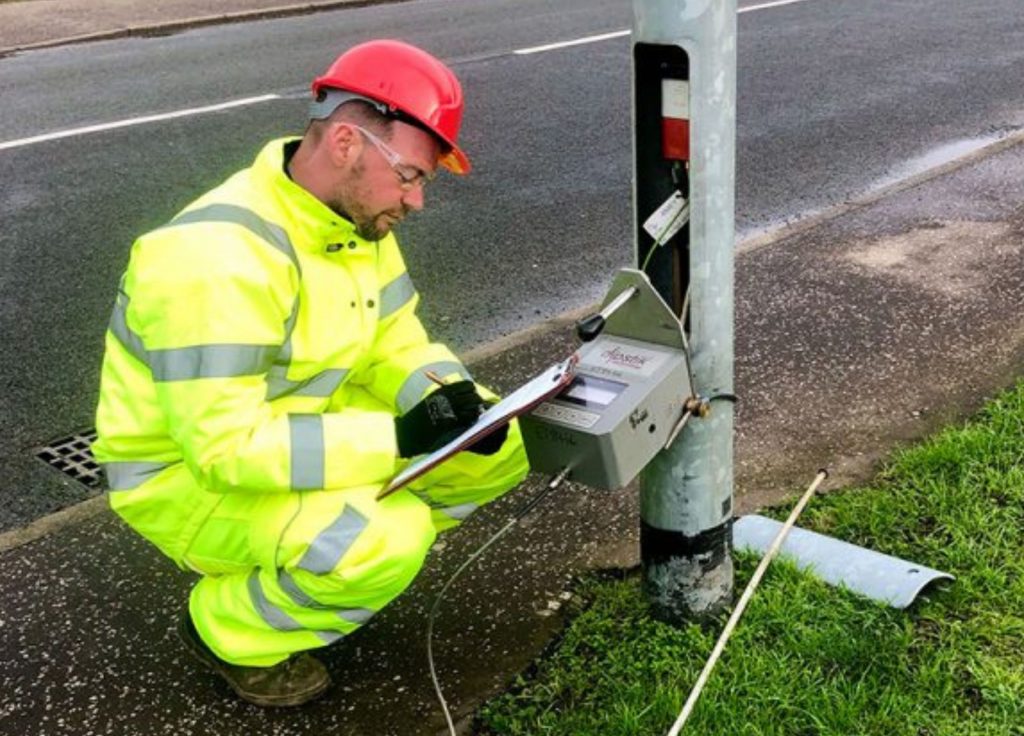
To test for fatigue, eddy current testing (Dipstik®) can be employed as a non-destructive method. This technique uses electromagnetic induction to detect flaws in conductive materials. It is particularly useful for detecting surface and near-surface cracks, which are often the initial signs of material fatigue. Eddy current testing is advantageous because it can be performed quickly and does not require the removal of coatings or paint, making it a practical choice for on-site inspections.
Corrosion can occur in multiple areas, such as the root, base, shoulder, and swage area. Fatigue, on the other hand, is often indicated by the number of repeat inspections where loss is found at a lower percentage. This can be a sign of material fatigue, which may necessitate an upgrade in the unit’s risk classification.
The Algorithm: A Multifaceted Approach
Our classification algorithm is designed to provide a well-rounded assessment of each unit’s structural state. Here are some of the key elements that contribute to the final score and classification:
- Defect Types: Defects can occur in various parts of a unit, including the column root, brackets, and lanterns. Traffic-related damages are also considered. Each defect type has its own scoring system, contributing to the overall risk score.
- Road Speed: The speed of the road where the unit is located is another crucial factor. Higher speeds may pose greater risks in the event of a failure, thus affecting the unit’s classification.
- Repeat Inspections: Multiple inspections over time can provide valuable insights into the unit’s structural integrity. For instance, repeat inspections where loss is found at a lower percentage can indicate material fatigue, prompting an upgrade in the unit’s risk classification.
- Imminent Hazard Criteria: In some cases, the unit may be in a condition that requires immediate action. This could be due to a combination of defects or other factors like leaning or looseness. Such cases are flagged as imminent hazards, leading to an immediate upgrade in classification.
- Material Deterioration: Factors such as corrosion and fatigue in steel are also considered. These can affect various parts of the unit, from the root to the bracket and even the shaft.
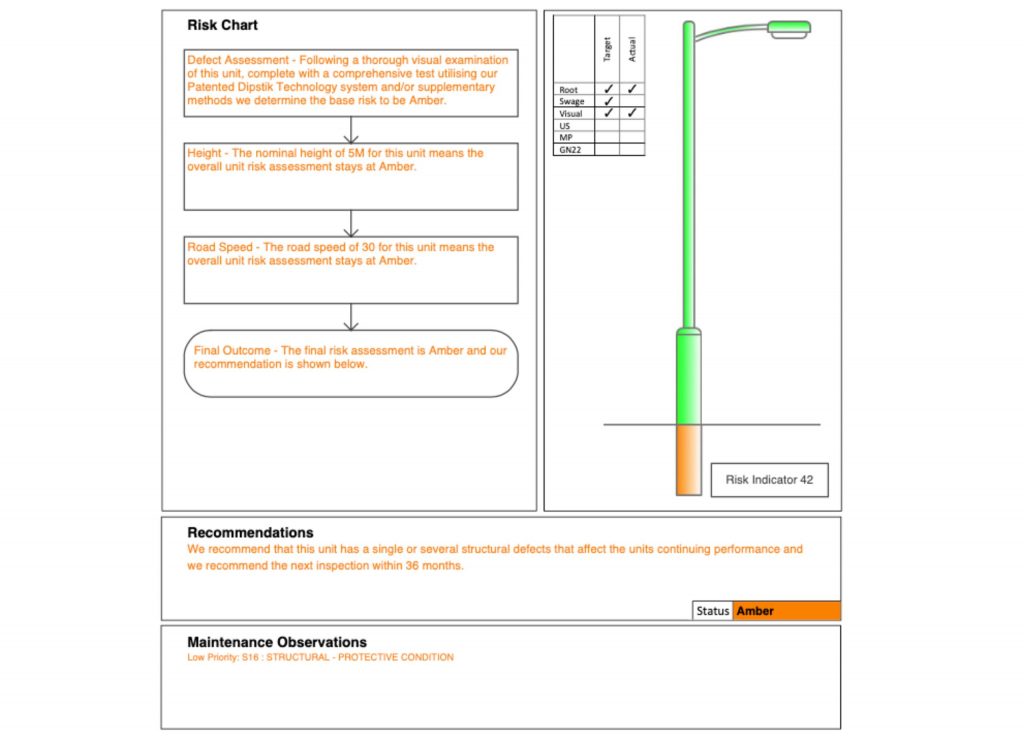
Simplifying Complexity: The Red, Amber, Green System
To make the final risk scoring more accessible and actionable, we categorise the outcomes into a Red, Amber, Green (RAG) system. Each colour corresponds to a level of risk and comes with its own set of recommendations and actions:
- Red (High Risk): Indicates significant defects and requires immediate action.
- Amber (Medium Risk): Suggests moderate defects and calls for scheduled maintenance or closer monitoring.
- Green (Low Risk): Implies minor or no defects and recommends regular inspection intervals.
Why a Holistic Approach Matters
The strength of a holistic approach lies in its ability to consider multiple variables, providing a more accurate and comprehensive understanding of each unit’s structural integrity.
This is crucial for effective risk management, as it ensures that all potential risks are adequately addressed. By adhering to the actions based on these final classifications, you can be confident that you’re taking the most accurate and effective steps to ensure public safety and infrastructure longevity.
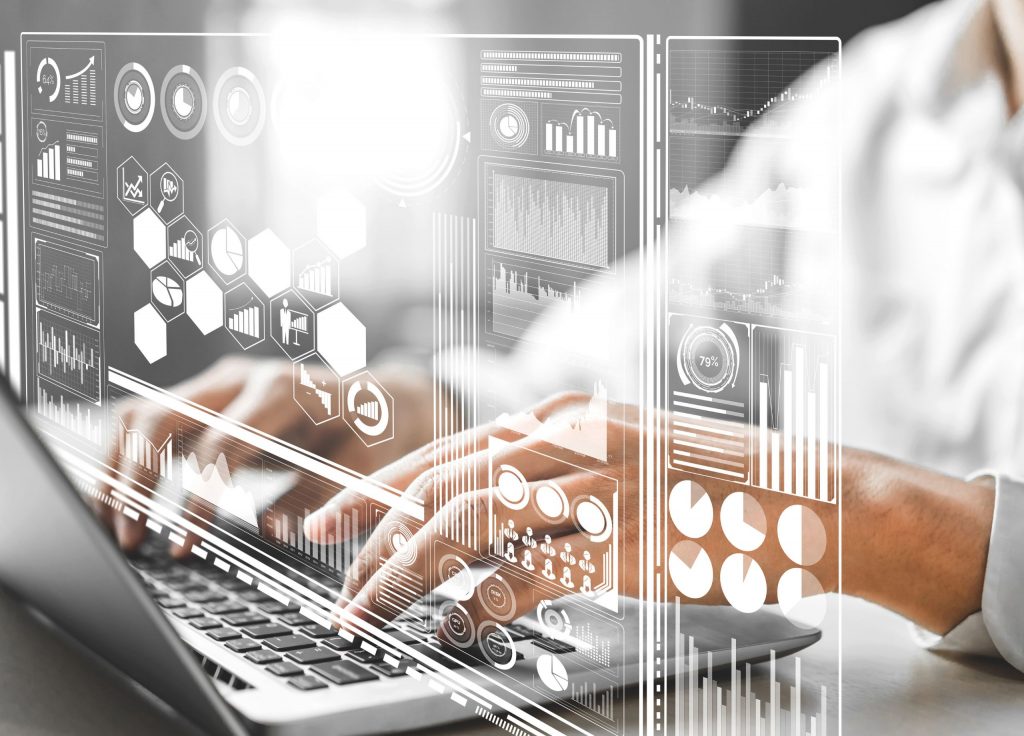
Final Thoughts
Asset classification is not a one-size-fits-all process. It’s a complex algorithm that considers a multitude of factors to provide the most accurate and comprehensive assessment possible. While it might be tempting to focus on a single defect or issue, doing so could lead to an incomplete understanding of the risks involved. A holistic approach, which considers a variety of variables, is essential for accurate and effective risk management.
By understanding the complexities involved in asset classification, you can better appreciate the robustness of our system. It’s designed to provide the most accurate information, guiding you towards the most effective course of action to ensure the safety and longevity of your infrastructure assets.