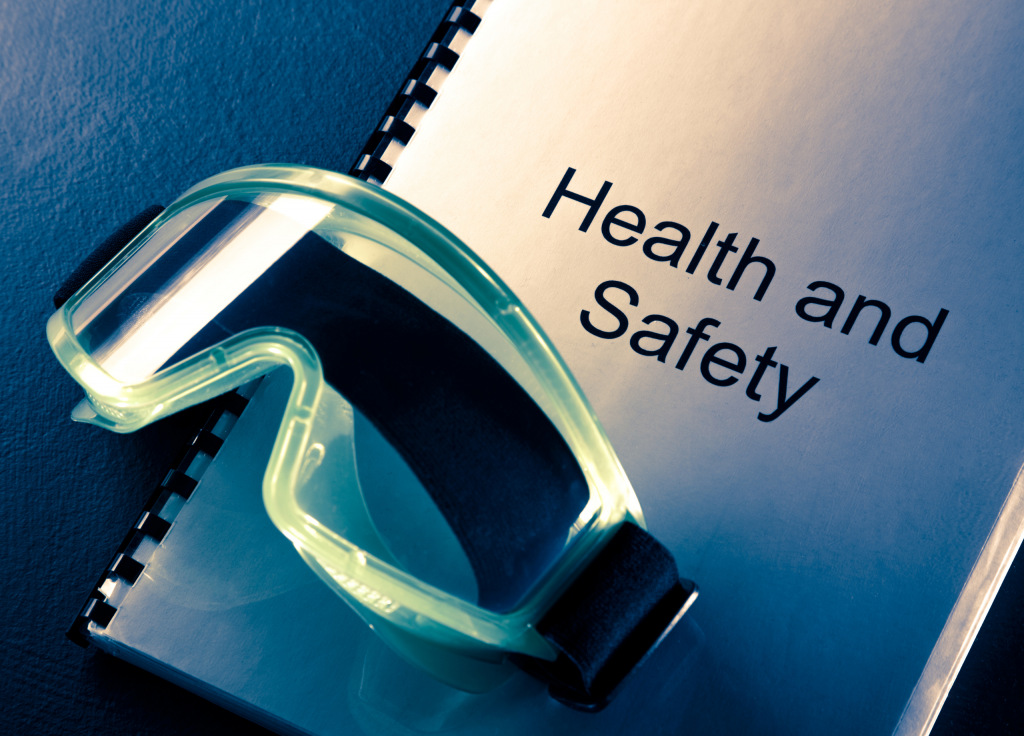
The construction sector, known for its dynamism and complexity, has to continually adapt to an array of regulations and guidelines. This adaptation is particularly crucial when it comes to protecting worker health and safety.
A recent case in point is the regulatory changes introduced by the EU, now adopted by the UK under REACH Regulations, concerning diisocyanates—a category of chemicals used widely in construction materials. Effective as of August 24, 2023, these new regulations call for a comprehensive understanding and proactive approach from industry professionals.
The Changing Regulatory Landscape: From Isocyanates to Diisocyanates
Isocyanates have long been on the radar of the Health and Safety Executive (HSE), with strict guidelines for their safe handling in construction. However, the spotlight has recently shifted to diisocyanates. These are chemicals closely related to isocyanates, but they pose similar, if not higher, health risks. The EU has recognized this by standardizing worker protection requirements for handling diisocyanates.
What You Need to Know About New Regulations
Exposure Limits:
- Introduction of long-term and short-term exposure limits.
- “Notations” indicating diisocyanates can be absorbed through the skin.
Health Risks of Diisocyanates: A Closer Look
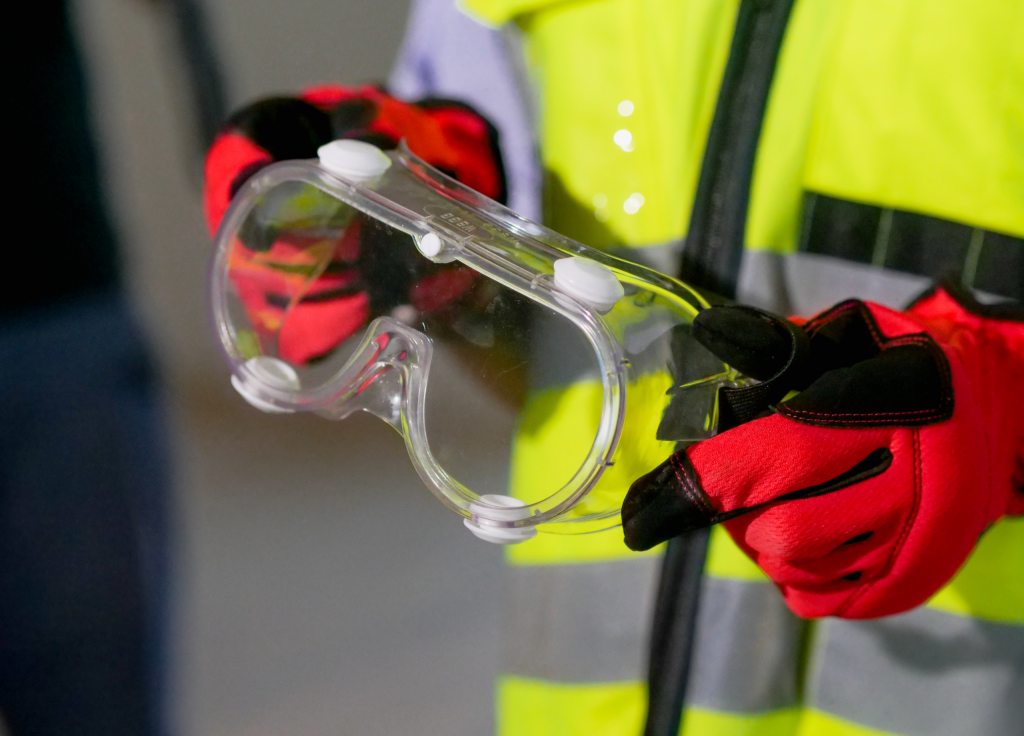
Diisocyanates are prevalent in various construction materials like cable jointing compounds and while isocyanates have been a known risk factor in construction and industrial settings, diisocyanates pose an even higher level of concern.
The ‘di-‘ prefix in diisocyanates indicates the presence of two isocyanate groups in the chemical structure, which can lead to higher reactivity and volatility. This amplified chemical activity elevates the risk of health implications such as occupational asthma, dermatitis, and eye irritation.
Furthermore, the newly introduced regulations have set stricter exposure limits for diisocyanates than those for isocyanates. The long-term occupational exposure limit for diisocyanates is significantly lower than that for isocyanates, emphasizing the increased risk and the urgent need for comprehensive protective measures.
Another factor that amplifies the risk of diisocyanates is their potential for skin absorption, as indicated by the new ‘notations’ in the regulations. This requires attention to protective measures beyond inhalation safeguards, including specialised Personal Protective Equipment (PPE) designed to prevent skin contact.
The combination of these factors—higher reactivity, stricter regulatory limits, and additional exposure routes—makes diisocyanates a pressing concern that necessitates immediate and rigorous risk mitigation strategies.
Training & Documentation: A Critical Pillar of Compliance and Safety
One of the most pivotal aspects of the new REACH regulations concerning diisocyanates is the emphasis on training and documentation. This is not merely a box-ticking exercise but a crucial step in ensuring the safety and well-being of all workers who may come into contact with these chemicals.
Comprehensive Training Programmes
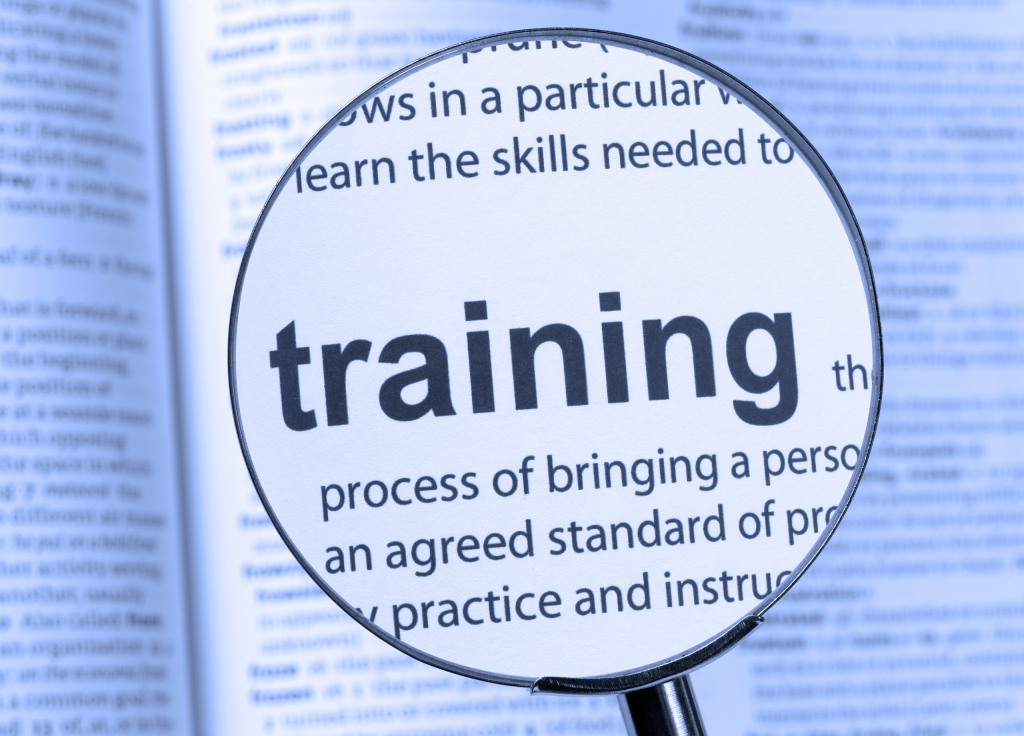
The regulations mandate that all workers who handle diisocyanates must undergo comprehensive training. This training is designed to equip workers with the knowledge and skills they need to handle diisocyanates safely. Topics covered in the training include:
- Identification and properties of diisocyanates
- Health risks and routes of exposure
- Safe handling procedures and emergency response protocols
- Proper use of Personal Protective Equipment (PPE)
It’s worth noting that this training must be delivered or overseen by an expert in occupational safety and health. This expert should have competence acquired through relevant vocational training, ensuring that the training is both rigorous and tailored to the specific risks associated with diisocyanates.
Regular Updates and Renewals
Training is not a one-off requirement. The regulations stipulate that documentation proving successful completion of this training must be renewed at least every five years. This ensures that workers’ knowledge and skills are kept up-to-date, reflecting any advancements in safety measures or changes in regulations.
Supplier Responsibilities
Suppliers also have a role to play in this training ecosystem. They are required to provide language-specific training materials and packaging labels. This ensures that workers, regardless of their native language, have access to the information they need to handle diisocyanates safely.
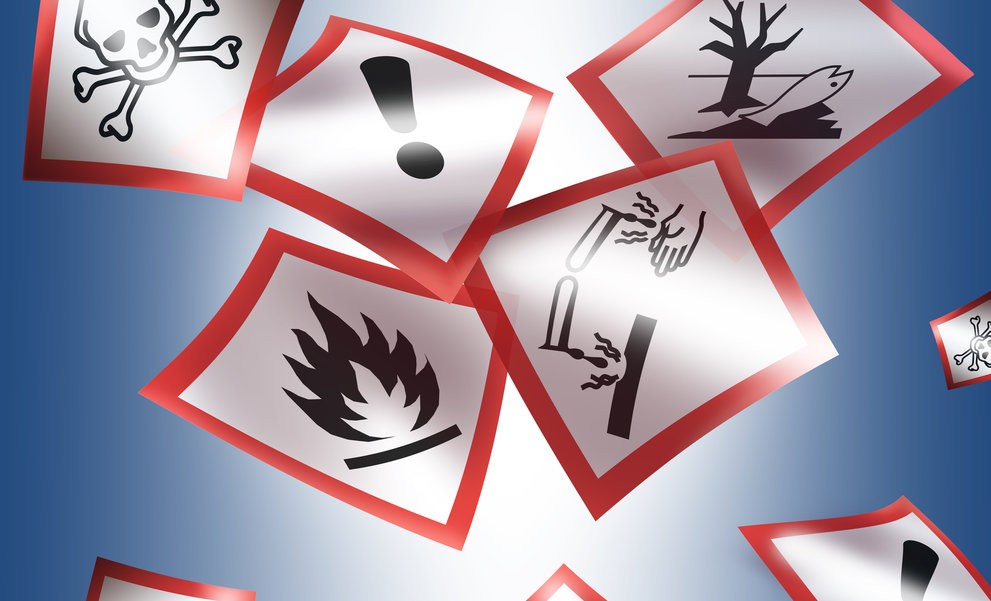
Record-Keeping and Documentation
Proper documentation is not just a regulatory requirement but also a best practice that can serve as evidence of due diligence in case of inspections or incidents. Employers must maintain records of training completion, and these records must be readily available for verification by regulatory bodies.
By adhering to these training and documentation requirements, construction firms can go a long way in mitigating the risks associated with diisocyanates. This is not just about regulatory compliance; it’s about safeguarding the health and well-being of every member of your team.
Proactive Steps for Ensuring Worker Safety
In order to align with the new regulations concerning diisocyanates, we are taking a multi-faceted approach to safeguard our team’s health and safety.
We are rolling out Training Programmes to provide comprehensive training for all relevant staff. Concurrently, we’re auditing and updating our existing Method Statements and Risk Assessments to integrate new control measures, such as specialised Personal Protective Equipment (PPE).
These actions are part of our ongoing commitment to not just meet, but exceed, regulatory requirements and ensure a safe and healthy working environment for our team.
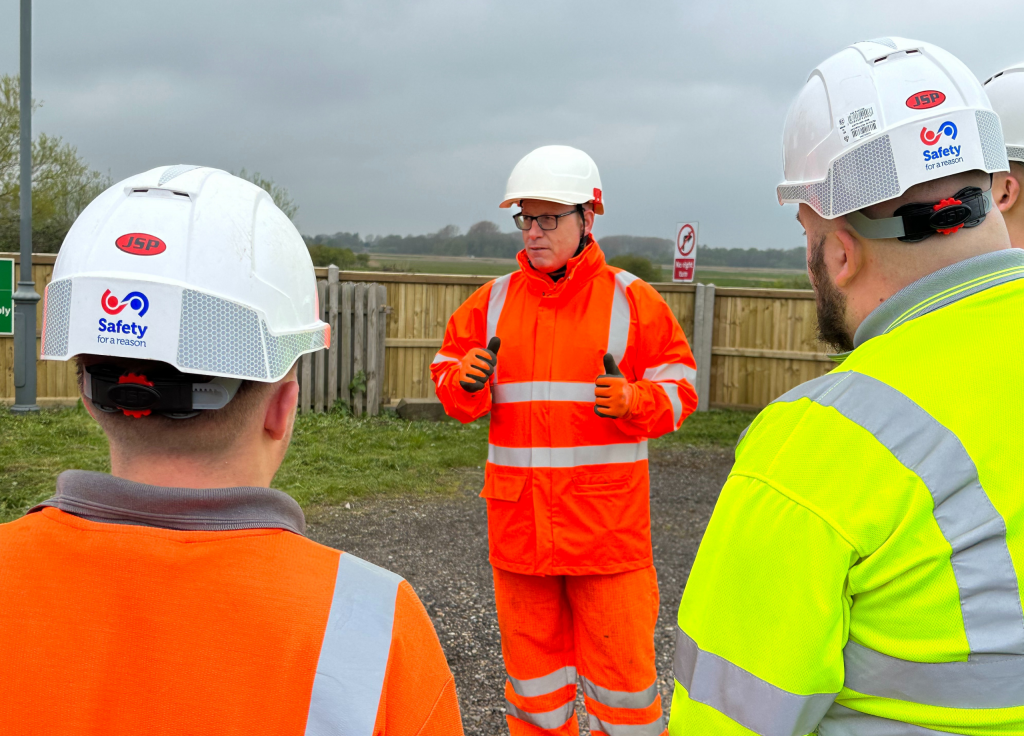
Final Thoughts
The new regulations related to diisocyanates are a wake-up call for the industry. They underscore the need for ongoing education, rigorous safety measures, and compliance mechanisms.
By taking these steps, we don’t just aim to meet regulatory requirements; we strive to exceed them, ensuring a safe and healthy work environment for our team.